PLC RANGES AVAILABLE
Allen Bradley Uses a different type of Programmable Logic Controller. These Different types of PLCS
perform specialized functions. This allows Allen Bradley to use the best PLC for your Company
specific needs.
- Micro and Nano Control Systems
- Pico Controller
- Micro800 Controller
- MicroLogix Controller
- Small Control System
- SLC 500 Controller
- SmartGuard 600 Controller
- Compact GuardLogix Safety Controller
- Compact Logix Controller
- Large Control System
- PLC-5 Controller
- GuardLogix Controller
- Softlogix Controller
- Control Logix Controller

PICO CONTROLLER
The Pico Controller performs simple logic, timing, counting, and real-time clock operations. For enhanced functionality and performance, the Pico GFX controller adds the use of a graphic display while offering advanced programming features like PID control, a high-speed counter, and Boolean sequences. Splitting the difference between a timing relay and a lowend programmable controller, the Pico controllers are ideal for relay replacement applications where simple control applications such as building, HVAC, and parking lot lighting, and applications in which cost is a primary design issue. The Pico controllers were designed with ease of use in mind. All programming and data adjustments can be done via the on-board keypad and display, or with Allen-Bradley PicoSoft and PicoSoft Pro configuration software.
Programming Software: Picosoft, Picosoft Pro
I/O Capacity: 32
Communication Port/Protocol: Allen-Bradley 1760-CBL-PC02 cable

MICRO 800 CONTROLLER
The smallest Controller with standard communication is available in this controller(Ethernet/IP). Expansion modules available (Input, Output, Communication Modules).
The controllers within this family are typically used on stand-alone machines or small process applications. The family offers five distinct controller types that are further customizable through add-on modules: Micro810, Micro820, Micro830, Micro850, and Micro870.
Programming Software: Connected Components Workbench(CCW)
I/O Capacity: 48
Communication Port/Protocol: Ethernet, EtherNet/IP, RS232 / RS485, USB type-B

MICROLOGIX CONTROLLER
In 2014, the MicroLogix family was introduced in response to address the need for a less expensive PLC solution to compete with other manufacturers and the first MicroLogix introduced was MicroLogix 1000 supporting several types of I/O combinations. The platform did not use a rack but instead, modules were connected at the end of the package. MicroLogix1000, MicroLogix 1100, MicroLogix 1200, MicroLogix 1400, and MicroLogix 1500 are different Micrologix Controllers. Micrologix Controllers without embedded analog I/O points provide 32 digital I/O points, while analog versions offer 32 digital I/O points and 6 analog I/O points. You can expand all versions with up to seven 1762 expansion I/O modules.
Programming Software: Rslogix500
I/O Capacity: 156
Communication Port/Protocol: Ethernet, EtherNet/IP, RS232 / RS485
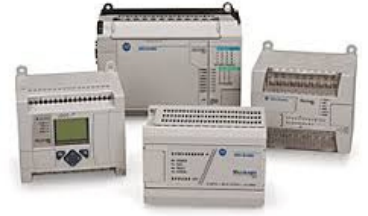
SLC500 CONTROLLER
The Allen-Bradley SLC 500 is a small chassis-based family of programmable controllers, discrete, analog, specialty I/O, and peripheral devices. The SLC 500 family delivers power and flexibility with a wide range of communication configurations, features, and memory options. The RSLogix 500 ladder logic programming package provides flexible editors, point-and-click I/O configuration, and a powerful database editor, as well as diagnostic and troubleshooting tools to help you save project development time and maximize productivity.
SLC was an acronym for Small Logic Controller and the first SLC500 released was an integrated package (commonly referred to as a shoe block PLC) containing the CPU, power supply, and I/O.
Each processor has one or two built-in ports for either EtherNet/IP, DH+, DH-485, or RS-232 (DF1, ASCII, or DH-485 protocol) communication.
Programming Software: Rslogix500
I/O Capacity: 4096/4096
Communication Port/Protocol: EtherNet/IP, DH+, DH-485, or RS-232 (DF1, ASCII, or DH-485 protocol)

SMARTGUARD 600 CONTROLLER
The SmartGuard 600 safety controller is a general-purpose programmable safety controller designed for safety applications that require some complex logic allowing for more advanced safety functionality. It features 16 safety-rated inputs, 8 safety-rated outputs, 4 pulse test sources, an optional EtherNet/IP™ port, and a DeviceNet connection that supports both standard and CIP Safety communication. Configuration and programming is accomplished through the built-in USB port.
RSNetWorx is used for DeviceNet to program the SmartGuard 600 and configure the DeviceNet network. Once inside RSNetWorx, you can launch an editor that will allow you to write function block programs for the SmartGuard 600 safety controller. No additional programming software is needed!
The SmartGuard 600 controller can control up to 32 Guard I/O modules.
Programming Software: RSNetworks
I/O Capacity: 32 Guard I/O Modules
Communication Port/Protocol: EtherNet/IP, DeviceNet, USB Port

COMPACT GUARDLOGIX SAFETY CONTROLLER
The Allen-Bradley Compact GuardLogix controller brings together the standard control functionality of the Logix Control Platform – a common programming environment, common networks and a common control engine – with the full range of integrated safety functionality of GuardLogix controllers in a smaller package. Ideal for mid-range applications, Compact GuardLogix controls up to eight axes of motion and supports the use of CompactBlock Guard I/O and POINT Guard I/O on Ethernet/IP, which creates a new option for machine builders looking to cost-effectively standardize on a single integrated safety control platform.
Compact GuardLogix safety controllers can provide:
- High functionality in an economical platform
- Rackless I/O for flexible installation
- Analog, digital and specialty modules that cover a wide range of applications
- Advanced system connectivity to EtherNet/IP, ControlNet, and DeviceNet Networks
- Truly integrated safety and motion control
Programming Software: RSLogix 5000
I/O Capacity: 32 Guard I/O Modules
Communication Port/Portocol: EtherNet/IP, ControlNet, and DeviceNet

COMPACT LOGIX CONTROLLER
The CompactLogix system is a Logix controller system widely used in medium and small industrial applications. These systems are used to control applications on the machine level. In general, a CompactLogix system is built by using a controller equipped with I/O modules and the DeviceNet communication network. It is manufactured with different specifications to meet different application needs based on the input type, output, memory type, communication module, enclosure type, and mounting options.
The CompactLogix system can support 16/30 I/O modules with a maximum of 3 I/O banks with 2 expansion cables. An additional CompactFlash card can be added for extra storage. All the CompactLogix systems can be mounted by using a DIN Rail.
The Logix system is equipped with a variety of communication ports, including the Ethernet/IP and ControlNet ports. The CompactLogix system can be controlled by using the RSLogix 5000 programming software.
Programming Software: RSLogix 5000
I/O Capacity: 16/30 I/O Modules
Communication Cable/Port: EtherNet/IP, ControlNet, RS232-RS485-RS422

PLC-5 CONTROLLER
The PLC-5 programmable controller stands at the center of a control architecture that brings together existing and future systems by means of networks such as EtherNet/IP, ControlNet and DeviceNet, and offers connectivity among SLC 500, ControlLogix, and MicroLogix controllers. Because they include embedded network connections, PLC-5 controllers enable your control architecture to be flexible enough to include cost-effective connections to a wide range of devices.
Programming Software: SoftLogix 5
I/O Capacity: 3072
Communication Cable/Port: EtherNet/IP, ControlNet, DeviceNet, Serial Communication(RS-232, RS-423, or RS-422A)

GUARDLOGIX CONTROLLER
A GuardLogix controller is a ControlLogix controller that also provides safety control. The GuardLogix system is a dual-controller solution that uses a primary controller and a safety partner. A major benefit of this system is that it is still one project, safety, and standard together. The safety partner controller is a part of the system, is automatically configured, and requires no user setup.
Programming Software: RSLogix 5000
Communication Cable/Port: USB, Serial Communication(RS-232, RS-423, or RS-422A) EtherNet/IP, ControlNet, DeviceNet.

SOFTLOGIX CONTROLLER
The SoftLogix controller is a soft controller based on the Logix Platform. The Logix platform provides a single integrated control architecture for discrete, drives, motion, process, and safety control. SoftLogix controllers use the Logix control engine and common development tools to provide high performance in an easy-to-use environment. The SoftLogix controller takes the control functions normally found in a dedicated programmable controller, encapsulates them in software, and runs them on a commercial operating system.
Programming Software: RSLogix 5000
Other Software: SoftLogix
Communication Cable/Port: Serial Communication, EtherNet/IP, ControlNet, DeviceNet.

CONTROLLOGIX CONTROLLER
ControlLogix provides a high-performance Control platform for multiple types of control. We can perform sequential, process, drive, or motion control in any combination with this single platform. Because the platform is modular, we can design, build, and modify it efficiently.
Programming Software: RSLogix 5000
Communication Port/Protocol: Serial Communication, EtherNet/IP, ControlNet, DeviceNet.


AB PLC – CPU MEMORY ORGANISATION
CPU memory is divided into two parts:-
- Data Files
- Program Files
Data files:-
System 0 -Manufacturer program
System 1 -Reserve file
Ladder 2 -Main user file
-ladder 3 to 255 for subroutine programs
Program files:-
0-Output – O –o/p status
1-Input – I –i/p status
2-Status – S2 –CPU data
3-Binary – B3 –Flag(memory bit)
4-Timer – T4 –Timer status
5-Counter – C5 –Counter status
6-Control – R6 –Specific data
7-Integer – N7 –whole no. data
8-Float – F8 –Decimal no.data
9 to 255 used to create new Program Files
AB PLC – ADDRESSING I/O

ADDRESSING BINARY(FLAG)

ADDRESSING OF PROGRAMMING INSTRUCTIONS

ADDRESSING OF SYMBOLS

COMMUNICATION PROTOCOLS COMPARISON

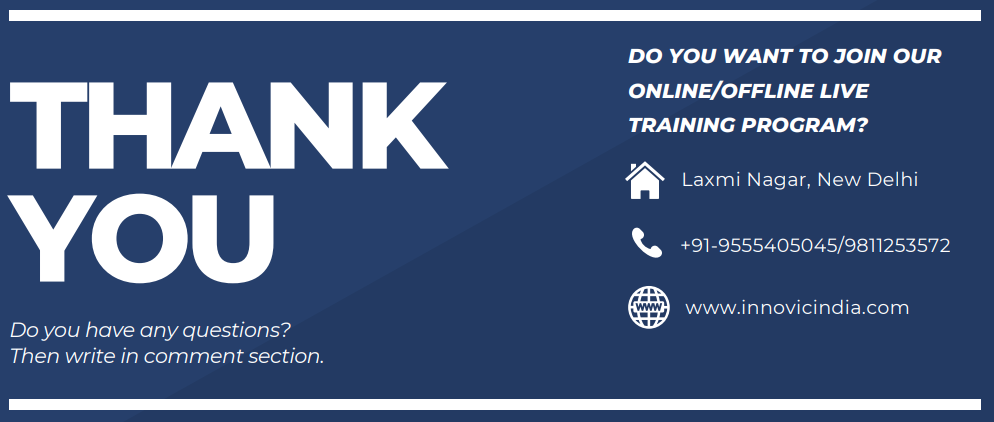